Introduction
We had an ASHP installed in our cottage in April 2022. I was impressed with the service provided by Optama staff throughout the process. We applied for the loan and cash back scheme with Home Energy Scotland. We contacted 3 companies for quotes. Optama was the middle one in terms of price. We decided to go ahead as we felt Chris from Optama had explained the options well and that the company were confident and prepared to install in an old property with potential challenges in designing and installing a system.
“There was a real sense of Chris’s commitment to alternative energy and helping us reduce our carbon footprint.”
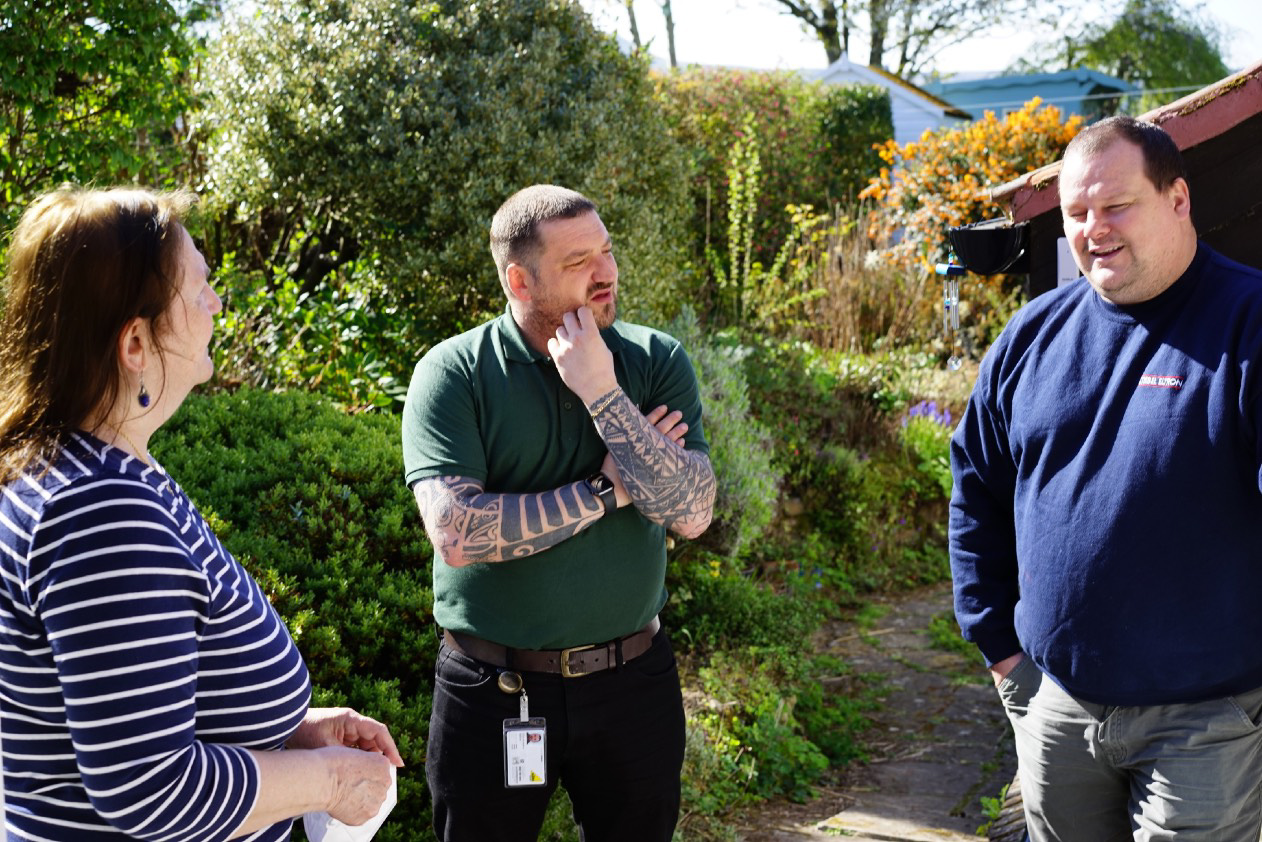
“There was no pressure to sign up and plenty of support and prompt responses to our questions via email and phone. Chris came across as an experienced and knowledgeable professional.”
Property details
Our house is unique with the front part over 200 years old with a thatched roof and thick stone walls, the rear of the building consists of a 2- phase extension in the 1990’s that incorporates part of a stone outbuilding and boundary wall and a timber, modern highceilinged extension with old pan-tiled roof and wooden board cladding. The building is a listed building and so we needed both Listed Building Consent and Planning permission to install a heat pump. This permission process incurred additional costs and a longer time to wait before we could start the installation and so we just missed out on the deadline to make a RHI claim.
Installation
Kenny from Optama contacted us and visited and organised the installation. I liked the way he involved us in discussing the best solutions to get the system retrofitted in our quirky cottage.
The contract was clear and had a 3 – stage payment structure. Deposit, main payment once the pump and radiators etc were delivered on site and final payment on completion of commissioning and provision of MCS certificate.
We agreed a start date that best suited us. We decided to stay in a local holiday cottage for the week so that we avoided the disruption of lifted floorboards and drilling. This proved to be very helpful as it gave the team a clear run to get on with the work and they chose to work longer days to complete the physical installation by Thursday evening.
I visited each day and was involved in discussing any adaptations to layout required to cause least disruption to the fabric of the building. This was one of our priorities. We had cleared out small pieces of furniture and furnishings prior to the start of the project and this enabled them to have easier access under floor- boards. I found the installation team to be friendly and respectful and clearly enthusiastic about doing their work well. They consulted me on the layout as the work progressed.
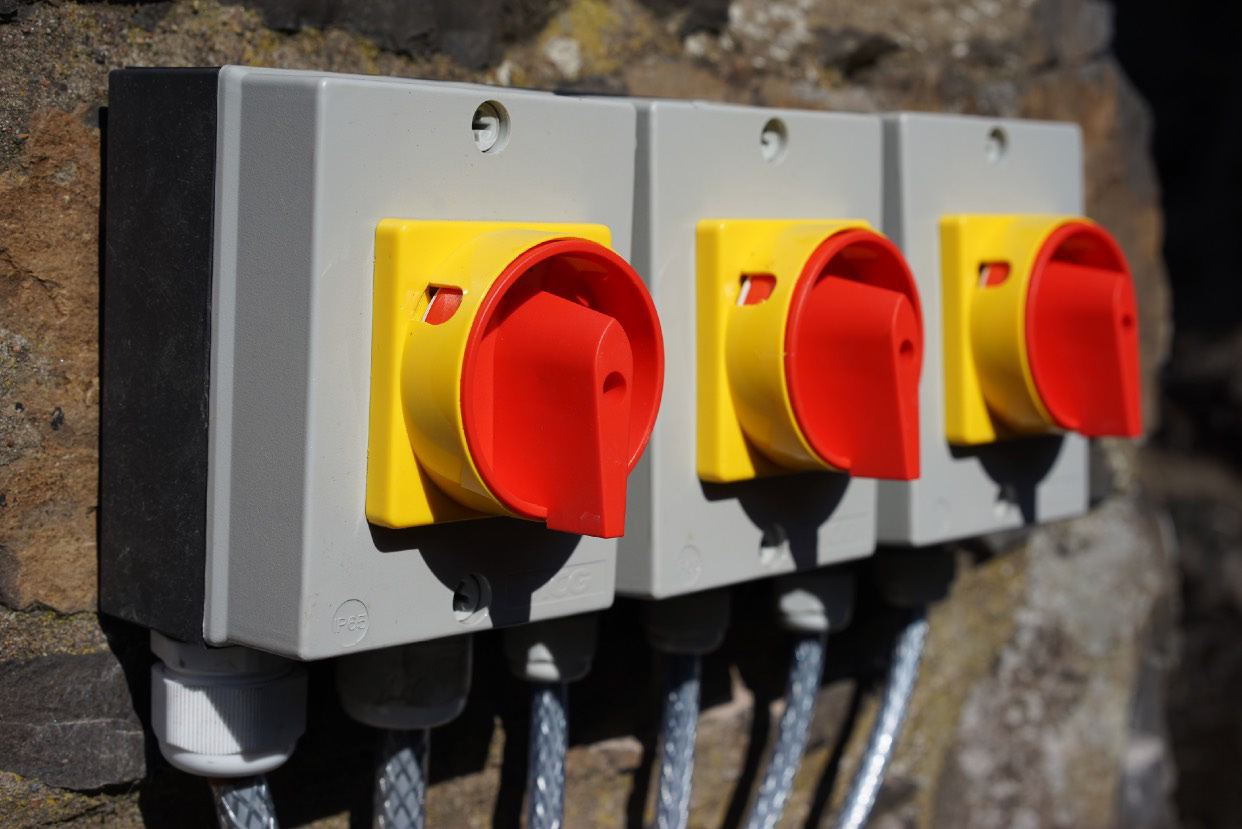
Fine tuning and commissioning
It was almost inevitable that the process of retrofitting an air source heat pump, new radiators and pipework in a non – standard building would generate some challenges in logistics and getting the balance right during commissioning the system.
On Thursday evening it seemed like all was running well and the team were finishing off insulating pipes and starting to clean up the site. Then the pump stopped circulating hot water in the central heating and we had lots of very hot water in the domestic hot water cylinder. There was a quick response from Kenny who also arranged for Alister from Stiebel Eltron to visit the next morning to address the issues. Alister took the time to explain what he was doing to set up the system and to answer some of my general questions about heat pumps and how
best to use the timer.
Alister made various adjustments and got the system running. I said I would monitor how the heating was working over the weekend with it running 24/7. There was still a problem with central heating temperature on the Saturday evening. I contacted Kenny and he arranged for someone to visit on the Monday and dealt with a couple of teething problems.
There was still an issue and so Kenny cancelled his course and visited that day to solve them. I let him know I was concerned about the system and commissioning and was given a full apology for the inconvenience and what I felt was a hundred percent commitment to solving it.
The main issue was an unusually large amount of air accumulating in the CH system. This was solved by fitting extra valves to release it. Kenny also fitted an extra radiator (free of charge) in the front sitting room to address my anxiety that the room would not be warm enough. Kenny and Alister visited again to check if I had any other questions and give advice.
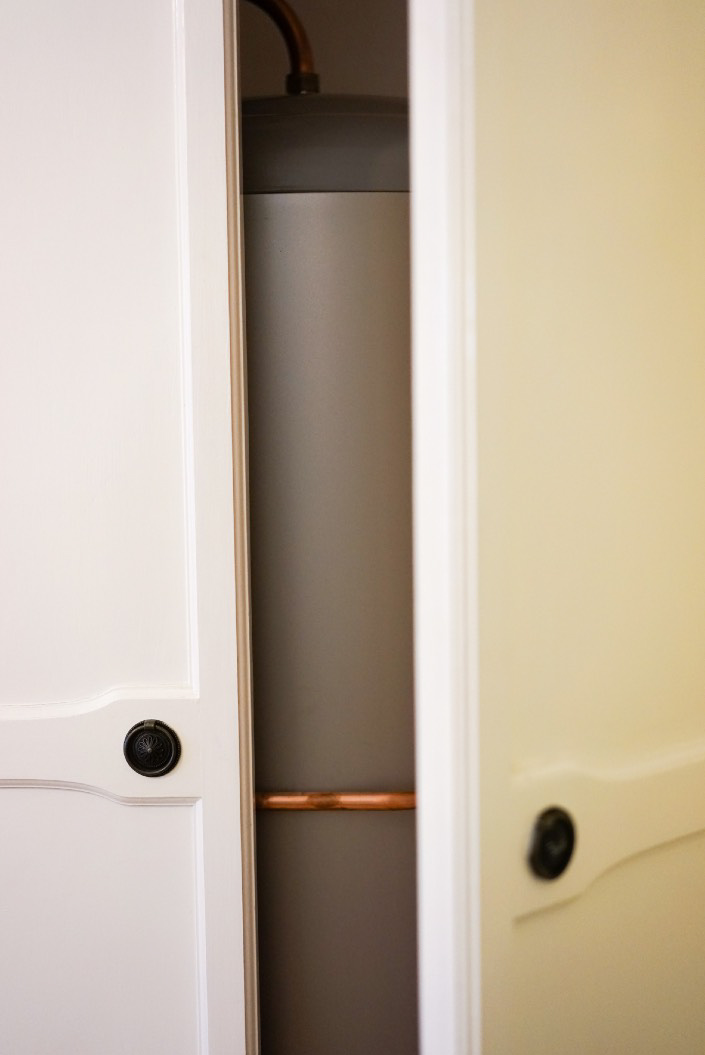
“I feel that this was an excellent service and gave me reassurance and confidence around having an air source heat pump.”
“I would highly recommend Optama as an installer. Their focus is on getting it right for the customer and on being willing to listen and respond with solutions.”
Thanks to everyone at Optama for their positive approach to supporting us on the journey to get rid of our gas CH boiler and install a Stiebel Eltron Heat pump.
Pam Gillespie
Auchtermuchty, Fife